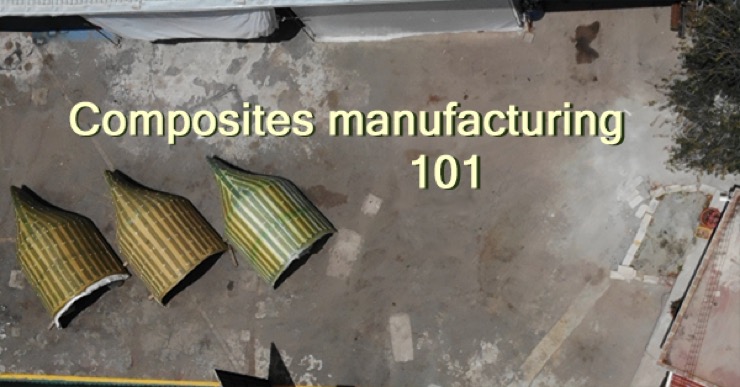
Our CCell-Wave paddles capture the power of ocean waves which is used to drive an electrolysis process that grows artificial coral reefs for coastal protection. Since this solution will need to be deployed all over the world, we have optimized our design to ensure everything can be manufactured by local boat builders, who we train remotely. They are taught how to produce the composite materials needed to make durable, high-quality paddles. These materials make the paddles light enough to be installed easily with a two-person team while still being strong enough to withstand hurricane season.
Unlike metal, which is one homogenous solid, composites contain at least two different materials. A standard composite material has three parts: fibres, matrix and core. The fibres provide high strength; the matrix holds everything together, giving a level of toughness so that the structure doesn't fracture and break apart, and the core brings stiffness while keeping the weight down. Within the CCell-Wave paddle, the core has a vital secondary role, buoyancy, which is due to its very low density. Having the paddle float at the correct orientation is essential for absorbing energy from the waves.
Composite materials can be anything from glass fibres with a polyester matrix to carbon nanotubes with an epoxy matrix. The fibres are extremely strong along their length and are held together by the weaker matrix. This means that you can control the strength of the different direction within your structure by aligning the fibres to withstand the high forces in critical directions. Unlike in metals, this allows you to reduce the “wasted” strength in off-axis directions. So with the right design, composite materials can provide the same durability and strength as metal while weighing and costing significantly less. The downside is that the design process is more arduous, and the manufacturing process is less well established.
Putting the three components of composite materials together provides several challenges: all of the glass fibres must be aligned as per the detailed design to ensure strength, the matrix must make up the correct proportion of the total material and must cover all of the fibres and core.
There are four methods which are commonly used to create structures like CCell-Wave, which are the same as the methods used to make most fibreglass boats.
This is a messy process which mixes short, chopped-up glass fibres with a liquid form of a matrix created by combining certain chemicals. This mixture then gets sprayed onto a mould and the liquid matrix sets over a few hours as its chemical components react. Whilst this is very easy to perform, it has major drawbacks, including significant health hazards for the manufacturers due to the chopped glass and vapours. There is also the issue of the random alignment of the short fibres which can produce weaker sections.
This method uses sheets of fibres which can be woven or stitched together so that they stay aligned in one or two specific directions. The glass sheets get laid onto a mould, and the resin matrix is painted on to bind everything together. A reasonably straightforward process, wet lay-up is much less messy than spray-up, but it's difficult to control how much matrix is used. This means the properties of the material and its quality can fluctuate dramatically, depending on the manufacturer's skill.
Pre-preg is similar to wet lay-up, except that the sheets of fibres are already infused with the matrix. They need to be stored carefully to avoid the matrix hardening before they can be used. The infused sheets get positioned onto a mould, covered with an airtight bag and placed under a vacuum at a consistently high temperature. This ensures that the layers compact correctly and have a proper distribution of resin, making a great composite. Unfortunately, this process is very costly; from the raw materials to their transportation to the heating of the entire mould.
This method combines the best parts of Wet lay-up and Pre-preg. The fibre sheets are laid on the mould while dry, then covered with an airtight bag. Here the force of a vacuum is used again, in a more sophisticated way, as the resin matrix is drawn into the structure via pipes. Carefully controlling this rapid process is crucial to ensure the matrix is evenly distributed. After matrix infusion, the structure is kept under vacuum, sometimes at high temperatures to speed up the process, until it's mostly set.
At CCell, we use Vacuum infusion to produce very high-quality parts while keeping raw material costs low. We engage in a significant amount of training for our already-skilled local manufacturers since this process is not widespread. Once taught, they can leverage their newly acquired knowledge to build other structures like high quality boats.
Environmental impact is essential to consider for the selection of materials and manufacturing of any product, and this is particularly important to us at CCell. Unfortunately, the choices available for matrix, fibre and core materials are not highly sustainable. On top of that, they are hard to recycle as they are a very complicated structure.
So, what can be done? Our approach so far has been to reduce the embodied energy in the structures. Embodied energy is the total energy associated with the production of something; this includes the extraction of raw materials, transport, manufacture, installation, and the end of its lifecycle. By reducing the transport required for the components of our paddle and manufacturing them locally, we have been able to begin reducing our impact.
However, we have much bigger plans in the works. Thanks to recent research and availability of materials, it is now possible to use cork, a natural and sustainable material, as the core of our structure. We are also looking at using resins for the matrix which are partially derived from plants rather than fossil fuels. The final key to the puzzle is natural flax fibres which may be able to replace our current glass fibres. Since the strengths of these replacement materials are lower, there is a lot of research and development still to do to make their use a reality, but we are very excited to start testing and pushing their limits.